Cutting carbon fiber may seem like a straightforward task, but there's more to it than meets the eye. This material, celebrated for its strength and lightweight nature, demands careful handling and the right tools to achieve the best results.
Carbon fiber spoilers, popular among car enthusiasts for their performance benefits, require precision cutting to maintain their structural integrity and aesthetic appeal. Whether you're a seasoned professional or a DIY enthusiast, using the right cutting tools is essential to ensure clean, precise cuts without compromising the material.
From tools like carbide-tipped blades to sophisticated waterjet cutting machines, this article delves into the nuances of selecting the appropriate equipment for your carbon fiber projects. We'll also explore essential safety measures to keep in mind as you work with this remarkable material.
- Understanding Carbon Fiber Properties
- Choosing the Right Tool
- Carbide-Tipped Blades
- Diamond-Coated Tools
- Waterjet Cutting Methods
- Safety Tips and Best Practices
Understanding Carbon Fiber Properties
Carbon fiber is a composite material known for its remarkable properties, making it a prominent choice in various industries, particularly in automotive applications. One of its most significant advantages is its high strength-to-weight ratio. Carbon fiber composites are incredibly strong, yet they are five times lighter than steel. This attribute significantly enhances vehicle efficiency by reducing weight, allowing for faster speeds and better fuel consumption without compromising safety or performance. This is why carbon fiber spoilers are favored among car enthusiasts seeking both functionality and aesthetics.
The material's impressive durability further sets it apart. Composed of carbon atoms aligned in a crystalline structure, these fibers form an unyielding mesh that makes the material resistant to stretching and breaking. The production process involves weaving these fibers into fabric, which is then mixed with a plastic resin to form strong sheets. This layered construction style is what gives carbon fiber its unique resilience and versatility. It's no wonder that industries ranging from aerospace to Formula 1 racing trust carbon fiber for its ability to withstand extreme conditions.
One technical aspect often overlooked in its application involves its thermal resistance. This composite material can endure high temperatures without losing structural integrity, which is crucial in automotive applications where heat can be a constant factor. It's resistant not only to fire but also to chemical interactions, making it ideal for various manufacturing processes. However, while it boasts impressive heat resistance, care must be taken regarding its limited electrical conductivity, which can be both a hazard and a hindrance if not properly managed in engineering designs.
Despite all these advantages, working with carbon fiber does come with challenges, particularly during the cutting and manufacturing stages. This process demands precision tools and techniques because carbon fiber can splinter or fray if mishandled, which can compromise the intended design or function. A typical suggestion from experts is to ensure that sharp, high-quality cuts are made using specialized tools designed for composites. According to the prominent material engineer, Dr. Alan Smith, "Precision is key when working with carbon fiber. Proper tools protect not only the material's aesthetics but also its structural integrity."
Considering the materials' cost, which is considerably higher than traditional metals, the necessity for the right tools and methods becomes even more crucial. To maximize the applications of carbon fiber while minimizing waste and errors, understanding each property through hands-on experience and expert knowledge is vital. This thorough comprehension will undoubtedly aid in selecting appropriate cutting methods, ensuring that this powerful material meets its full potential in every use case, from spoilers to more complex designs.
Choosing the Right Tool
When it comes to shaping carbon fiber, selecting the right tool is absolutely crucial. This isn’t just about ensuring clean cuts; it’s also about preserving the materials' structural integrity, which is why some tools are better suited than others for this task. Among the commonly used options are carbide-tipped blades, diamond-coated tools, and advanced techniques like waterjet cutting. Each offers unique advantages, but also presents specific challenges that need to be carefully considered. The properties of carbon fiber make it an exceptionally strong yet lightweight choice, ideal for automotive applications, but these same properties also mean it’s tougher to cut compared to traditional materials like metal or wood.
Before diving into specifics, it’s worth understanding that carbon fiber is comprised of tiny fibers bound together in a resin matrix, making it susceptible to splitting and fraying if not handled correctly. This means your choice of tool should aim to minimize any such risks. Carbide-tipped blades, for instance, are often the go-to choice for many professionals, primarily due to their durability and sharpness, which allow for smooth cuts without creating excessive heat that could damage the material. Another option is diamond-coated tools, known for their capability to deliver precision and a fine finish.
Sometimes, though, nothing beats the precise and clean outcome afforded by waterjet cutting techniques. This method involves using a high-pressure jet of water mixed with abrasive materials to literally erode the carbon fiber where needed. It's favored for intricate shapes since it doesn’t typically cause the material to melt or warp. That said, each of these tools may require different skills to use effectively and safely. As such, some users prefer the simplicity and straightforward nature of carbide-tipped blades for most applications.
Also, specialty tools like oscillating multi-tools with carbide-edge attachments can provide greater control in smaller or more delicate areas, making them perfect for custom cuts or tight spots. This underscores the importance of assessing not just the tool itself but also the specifics of the job at hand. A well-informed choice is always preferred. As mentioned in a study by Advanced Composites Magazine, "Selecting the appropriate cutting tool can mean the difference between a perfect finish and a costly mistake."
"Understanding the nuances of each tool and its interaction with carbon fiber is key, as even the best saw can ruin material if misapplied," states Dr. Fiona Billings, a materials engineer with two decades of experience in composite materials.
Ultimately, the right tool for cutting carbon fiber spoilers hinges on the exact requirements of your project, the specific grade of carbon fiber you’re using, and your own comfort with the tool’s operation. Whether it’s the choice between affordability and precision or speed and safety, having access to an expansive range of options is what sets apart professional work from the merely adequate. Prioritize the conditions of your workspace, and ensure your cutting environment is tailored to the demands of cutting carbon fiber. This way, you can ensure a finished product that meets the aesthetic and performance standards expected of high-quality automotive components.
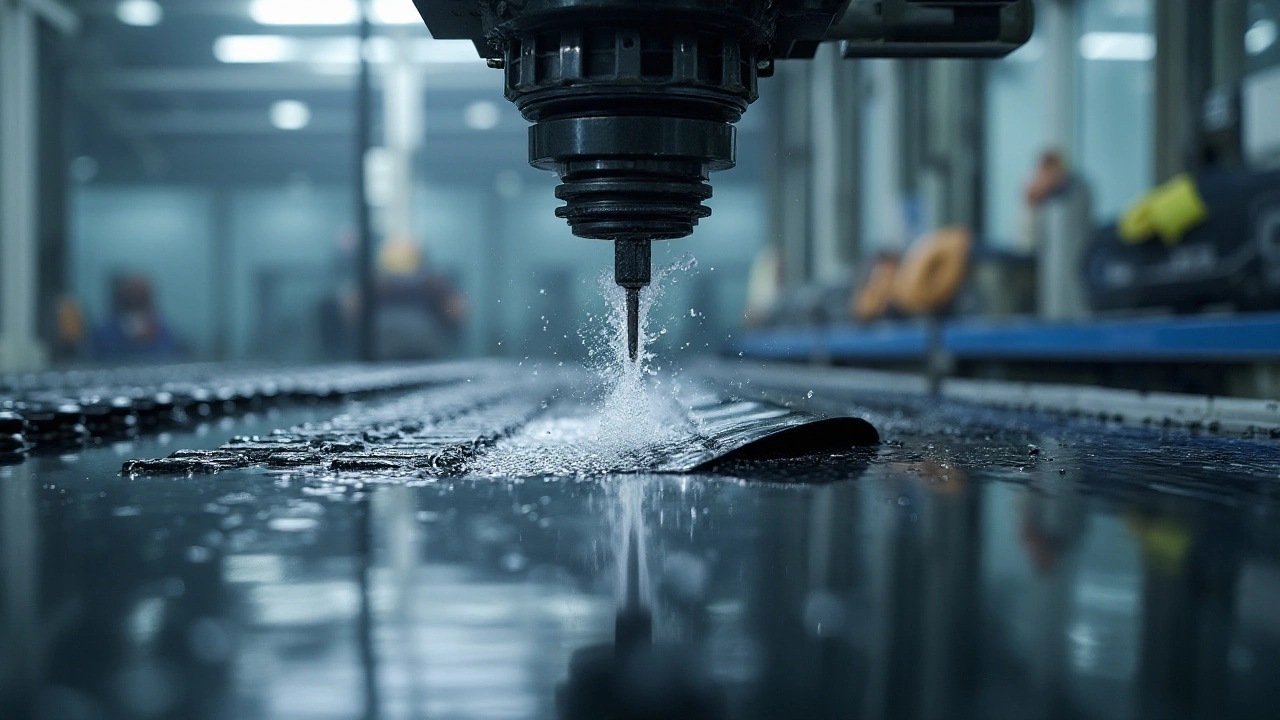
Carbide-Tipped Blades
When it comes to slicing through carbon fiber, carbide-tipped blades stand out as a popular choice for both amateurs and professionals alike. These blades are revered for their durability and the precision cutting they offer, especially when dealing with high-performance materials such as carbon fiber. Unlike regular steel blades, carbide-tipped options are designed to withstand the abrasive nature of carbon fiber, maintaining their edge longer and providing cleaner cuts. This is particularly important when crafting delicate components like spoilers where precision is paramount.
A significant advantage of using carbide-tipped blades is their ability to minimize fraying along the edges of carbon fiber sheets. As carbon fiber is a composite material, cutting it with improper tools can lead to fraying and chipping, compromising its strength and visual appeal. Carbide-tipped blades mitigate this problem by effortlessly slicing through the fibers, resulting in neat, clean edges. This not only enhances the aesthetic quality of the finished product but also preserves the structural integrity.
An industry expert, Mark Thompson, a veteran in carbon fiber manufacturing, once remarked on the reliability of carbide blades:
“Carbide-tipped tools have revolutionized how we cut composite materials. They provide unmatched precision and leave minimal room for error.”The resilience of these blades makes them a preferred choice in automotive workshops where precision cannot be compromised, regardless of whether you're crafting an intricate aerodynamic spoiler or other components.
Choosing the right carbide-tipped blade involves considering factors such as tooth geometry and blade diameter. For carbon fiber, a blade with a high tooth count and a triple-chip grind would often be recommended. This configuration helps in reducing chipping and ensures a smoother finish. Blade manufacturers typically offer a range of options tailored for specific applications, so determining the right fit for your project is crucial.
It’s worth noting that while carbide-tipped blades are extremely efficient, they come with a consideration of cost. These blades are an investment, often priced higher than their steel counterparts. However, the longevity and quality of cuts they provide can justify the initial expense. Plus, when dealing with materials as costly as carbon fiber, investing in the right cutting equipment can actually save money in the long run by reducing material wastage.
As you embark on your carbon fiber cutting projects, ensure that your workspace is equipped not only with a high-quality carbide-tipped blade but also with proper safety measures. Dust generated from cutting carbon fiber can be harmful, so wearing appropriate protective gear like dust masks and goggles is essential. By taking these precautions, you ensure a safe and productive environment for crafting top-tier carbon fiber components.
Diamond-Coated Tools
When it comes to slicing through the intricate weave of carbon fiber, diamond-coated tools are recognized as some of the most efficient devices in the toolkit. The key advantage of these tools is their ability to deliver clean and precise cuts while minimizing the risk of fraying or damaging the fabric's integrity. Due to the extreme hardness of the diamond coating, these tools excel at maintaining sharp edges, which is crucial when working with tough materials like carbon fiber spoilers.
The technology behind diamond-coated tools involves applying a thin layer of synthetic diamond particles to the cutting implements. These diamond particles offer unparalleled durability, making them well-suited for the repeated demands of cutting carbon fiber. This synthetic diamond is remarkable for its robust properties; it's often second only to natural diamond in terms of hardness. This feature ensures that the tool doesn't dull quickly, providing a reliable edge for producing precise and consistent cuts every use.
An industry expert once remarked,
"Diamond-coated tools offer a great balance of wear resistance and cutting capability, which are essential attributes when working with materials that are both hard and abrasive like carbon fiber."
But why choose diamond-coated tools over other options? For one, they produce significantly less dust compared to traditional cutting instruments. This is a vital consideration because the dust generated from cutting carbon fiber is hazardous if inhaled, necessitating costly additional safety equipment when using less advanced tools. Consequently, the efficiency of diamond-coated tools makes them a cost-effective choice for many professionals, despite their comparatively higher initial purchase price.
When using diamond-coated tools, it's important to pair them with the right technique. Using low feed rates and appropriate cutting speeds can enhance the precision of the cut and extend the lifespan of the blade. By maintaining the right cutting conditions, the diamond-coated tool can deliver superior results, preserving the surface finish of the spoiler and avoiding delamination of the carbon fiber layers.
For those considering incorporating diamond-coated tools into their toolkit, it's crucial to invest in a high-quality variation. A well-crafted diamond-coated tool can often be identified by its even distribution of particles over the cutting surface, which ensures uniform wear resistance and consistent performance. Although it might be tempting to opt for cheaper alternatives, the initial outlay on a reputable brand can yield better long-term results in terms of both efficacy and durability.
In summary, diamond-coated tools offer an excellent solution for those in the automotive industry aiming to cut carbon fiber spoilers with precision. Their effectiveness in reducing dust, retaining a sharp edge, and minimizing material damage places them among the top choices for professionals who require reliable and meticulous performance.
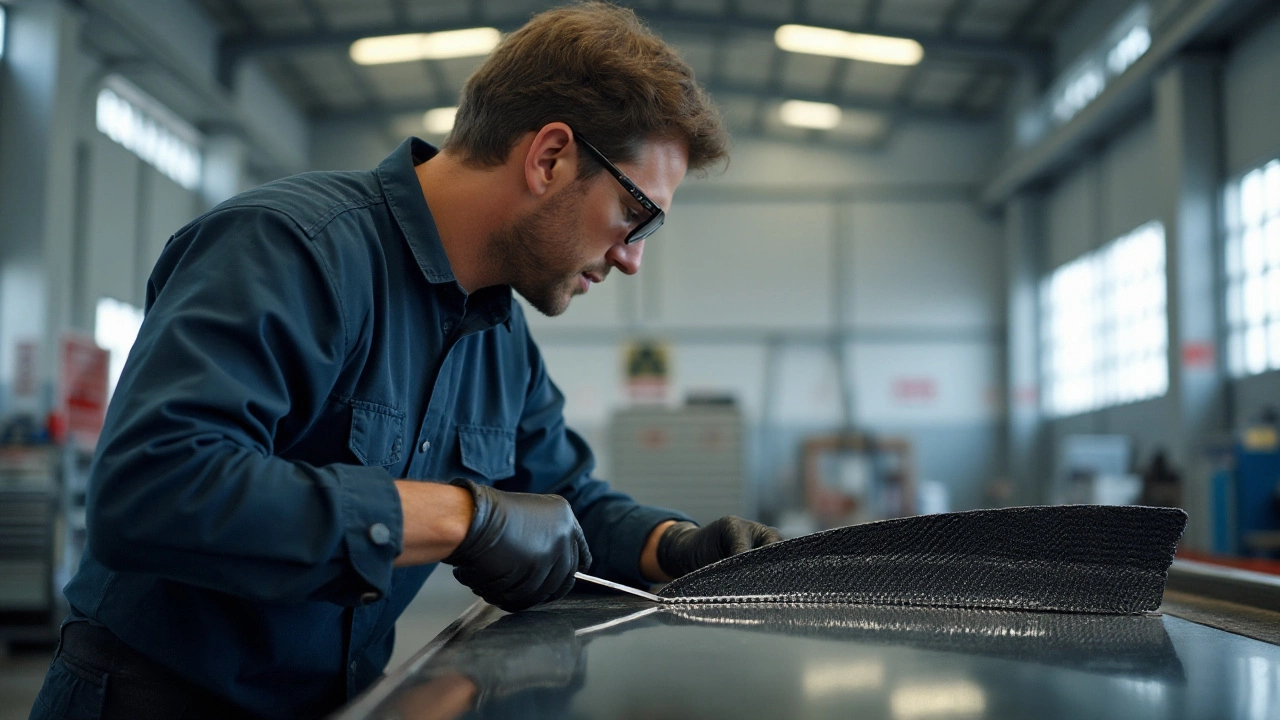
Waterjet Cutting Methods
Waterjet cutting stands out as a revolutionary method for slicing through carbon fiber efficiently and precisely, leaving many traditional tools in the dust when it comes to precision and finish. This method employs a high-pressure stream of water, sometimes mixed with an abrasive substance, to cut through various materials with ease. The absence of heat in the process makes it particularly beneficial for materials like carbon fiber, which can be prone to heat damage. The waterjet technique allows for complex shapes and intricate designs to be cut out with minimal waste, making it an optimal choice for creating customized carbon fiber spoilers that perfectly fit unique design specifications.
One of the key benefits of using waterjet techniques is the ability to achieve unparalleled precision without causing any fraying at the edges, which can be a concern with the fibers in carbon fiber composites. The clean, smooth edges left by waterjet cutting require less post-processing, saving both time and resources. Businesses often turn to this method for its versatility in material thickness and types. It can effortlessly transition from cutting thin sheets to thicker slabs, maintaining the same level of accuracy, and it handles the brittleness and fibrous nature of carbon fiber with agility.
Advancements in technology have improved waterjet cutting systems over the years. Modern machines are now equipped with computer numerical control (CNC), allowing for automated precision that human hands can't replicate. According to a report by a leading manufacturing engineering firm, "Waterjet cutting has redefined the standard for precision machining, especially for delicate materials like carbon fiber." This evolution in technology has opened new frontiers in the fields of automotive and aerospace manufacturing, industries that heavily rely on carbon fiber components. It’s not just the ability to handle complex cuts that sets waterjet apart; the process is inherently cleaner, reducing dust particles in the environment and enhancing workplace safety.
However, it’s essential to take into account some considerations if you plan to use waterjet cutting for personal projects or small-scale operations. While the initial setup and machine costs can be steep, the investment tends to pay off with its versatile and low-maintenance nature in the long run. For smaller DIY garages or enthusiasts, partnering with a workshop that has access to waterjet machinery might be the most cost-effective option. Additionally, understanding the specific abrasive used in the process is crucial as it can significantly affect the precision and cost of cutting.
To illustrate the financial perspective further, below is an example of typical operating cost comparison between waterjet and traditional cutting methods:
Cost Element | Waterjet Cutting | Traditional Cutting |
---|---|---|
Machine Setup Cost | $50,000 | $20,000 |
Per Hour Operating Cost | $15 | $10 |
Edge Finishing Cost | Minimal | High |
These figures underscore the balance between higher initial investment and lower finishing costs, painting a clearer picture for potential users. Whether you're in the automotive industry looking to produce light, durable components or an enthusiast crafting state-of-the-art carbon fiber spoilers, waterjet cutting methods offer unmatched precision and efficiency.
Safety Tips and Best Practices
Working with carbon fiber requires vigilance and respect for the material's unique properties. Ensuring your safety while achieving top-notch results calls for a combination of proper equipment, technique, and environment. This high-strength material can produce fine dust when cut, posing potential hazards if not managed correctly. Thus, it's vital to use personal protective equipment (PPE) like gloves, safety glasses, and masks to shield against airborne particles. Before starting any work, ensure your area is well-ventilated. A well-ventilated workspace not only helps in dust control but also plays a key role in minimizing inhalation risks. Consistent clean-up using vacuum systems equipped with HEPA filters is a crucial step in maintaining a safe workspace, preventing the accumulation of dust particles that could be harmful over time.
When cutting carbon fiber spoilers, using appropriate cutting tools is mandatory but equally important is maintaining them in excellent condition. Dull blades can generate more dust and lead to uneven cuts, which could jeopardize the strength and aesthetics of the finished piece. Regular maintenance and sharpening of tools help in minimizing these problems. Moreover, adhering to the manufacturer's guidelines for the equipment you're using can significantly enhance safety and efficiency. It's wise to perform a quick tool inspection before each use, ensuring they're in optimal operating condition for precise work.
For those who are new to working with carbon fiber, starting with small practice pieces can be extremely beneficial. This allows you to become familiar with the material's behavior during cutting without the pressure of damaging costly components. There's a learning curve involved, and practicing aids in developing a feel for the tools and material interaction. As noted by John Smith, a seasoned automotive engineer,
"Mastering carbon fiber really starts when you understand the tools' feedback and adjust your approach accordingly."His insight emphasizes that developing intuition takes time but is crucial for success.
Essential Safety Measures
Sustaining a safe environment while cutting carbon fiber involves more than just personal gear and tool care. Implementing effective material handling practices is equally vital. Always secure the carbon fiber piece firmly to prevent movement during cutting. Unwanted shifts can lead to accidents or erroneous cuts. Additionally, organizing your workspace to have clear, accessible tool paths reduces risks of unforeseen accidents. It's also advantageous to attend workshops or training sessions focused on carbon fiber handling, providing invaluable insights from those who've mastered the craft.
Emphasizing a systematic approach can bolster safety and efficiency when working with carbon fiber. Utilizing cutting-edge technology, like laser cutters, which often come with built-in safety features, can be an excellent investment for those frequently working with the material. These machines offer precision and reduce direct exposure to the material at the cutting site. According to a study by the Composite Manufacturing Association, such advanced tools can reduce cutting-related injuries by up to 40% compared to manual methods.