Carbon fiber is a revolutionary material known for its lightweight and incredibly strong properties, making it a favorite in industries ranging from aerospace to automotive. Particularly, enthusiasts often seek carbon fiber spoilers for their vehicles due to their impressive performance benefits and sleek look. Naturally, if you're embarking on a project involving carbon fiber, you might wonder: can a Dremel be used for cutting?
In this article, we'll explore the feasibility and techniques of using a Dremel tool to cut carbon fiber, often surprising many with its efficiency and precision. Whether you're customizing auto parts or tackling a home DIY project, understanding the right approach can make all the difference. We’ll walk you through the essential steps, offer safety advice, and share pro-tips that bring out the best results. Let’s dive into the world of carbon fiber and unlock its potential.
- Understanding Carbon Fiber and Its Uses
- Why Use a Dremel for Cutting?
- Step-by-Step Guide to Cutting Carbon Fiber
- Safety Measures When Working with Carbon Fiber
- Finishing and Aftercare Tips
Understanding Carbon Fiber and Its Uses
Carbon fiber is an extraordinary composite material that has redefined the boundaries of what lightweight yet robust structures can achieve. Consisting primarily of carbon atoms bonded together in long chains, these fibers are subsequently woven into a fabric to create an incredibly strong and lightweight material. One of the most remarkable properties of carbon fiber is its weight-to-strength ratio, which is far superior to traditional metals such as steel and aluminum. For this reason, it's no surprise that industries as varied as aerospace, sports equipment, and the automotive world have embraced carbon fiber for its ability to enhance both performance and fuel efficiency with cutting-edge advantages.
The automotive industry, in particular, sees significant benefits from incorporating carbon fiber. Car enthusiasts and manufacturers alike value carbon fiber spoilers due to the material's ability not only to reduce the weight of the vehicle but also to improve aerodynamics. This dual impact results in better fuel efficiency and enhanced speed capabilities. The impact of carbon fiber on the automotive world is underscored by its presence in high-performance cars, including race cars, where every gram saved can make a world of difference in outcomes.
The Revolutionary Impact on Various Industries
Beyond automobiles, carbon fiber's potential stretches into the realm of aeronautical engineering and space exploration. Here, reducing weight is crucial for efficiency during flights and launches. In these sectors, carbon fiber composites often replace aluminum, leading to significant improvements in fuel consumption and load capacities. A testament to its effectiveness can be seen in advanced airplane designs that utilize hundreds of carbon fiber components to reduce overall aircraft weight while maintaining structural integrity. Such an impressive feat has accelerated global travels and opened pathways to even more challenging expeditions beyond our atmosphere.
"Material prowess in the modern world is no longer about sheer strength; it's about a balance of strength and agility. Carbon fiber represents the future of this equilibrium." — Materials Science Journal
The flexibility of carbon fiber continues to unlock innovative uses across various domains. In the world of sports, carbon fiber enriches the performance of equipment. Tennis rackets, bicycles, and even skis use carbon fiber to deliver unmatched strength without adding extra weight, allowing athletes to push performance boundaries imaginatively and dynamically. Similarly, medical devices employ carbon fiber due to its biocompatibility and radiolucency, making it ideal for prosthetics and supports that need to be stable yet lightweight without interfering with medical imaging technologies.
Advantages Over Traditional Materials
When evaluating the pros of carbon fiber, one cannot overlook its durability, resistance to corrosion, and ability to withstand harsh environmental conditions. Carbon fiber’s resistance to chemical and water attacks makes it an excellent choice for even the most demanding environments, ranging from undersea equipment to constructions situated in aggressive weather locales. Its adaptability and resilience translate into long-lasting applications that require lesser replacement and maintenance intervals when compared to metal alternatives.
To capture these transformational benefits, various sectors continue to research and expand carbon fiber's applications. As a foundation material that sparks innovations, its potential seems limitless. As the search for sustainable and futuristic resources progresses, carbon fiber stands ready to redefine how industries approach weight, strength, and efficiency in creative, groundbreaking ways. Whether used in crafting intricate designs or powering next-gen propulsion systems, carbon fiber proves its place as a visionary material in the modern age.
Why Use a Dremel for Cutting?
The idea of cutting carbon fiber material might initially seem daunting, but a Dremel tool opens avenues that make this task more approachable. One of the primary reasons people reach for a Dremel is its versatility. These rotary tools boast myriad attachments and accessories that transform the humble Dremel into a power-packed, multipurpose cutting device. What truly sets the Dremel apart, especially for projects like crafting carbon fiber spoilers, is its ability to make precise and controlled cuts. The high-speed rotation of its bits ensures smooth, clean edges, minimizing fraying that could compromise the integrity of your carefully planned project.
A compelling aspect of the Dremel is its user-friendly nature. Even those who are relatively new to DIY or automotive customization projects will find that the Dremel’s ergonomic design and intuitive operation provide confidence to handle tasks that might otherwise seem reserved for seasoned craftsmen. The learning curve is gentle, allowing for a rewarding experience right from the start. Moreover, the Dremel's compact size proves indispensable for detailed work, allowing you to reach into tight spots and niches that might challenge bulkier tools. This convenience is particularly advantageous in intricate designs often seen in carbon fiber applications.
Precision and Versatility
For those working on automotive projects, including car enthusiasts customizing spoilers, the precision a Dremel brings is unparalleled. Whether you're trimming excess material or creating exact openings, the tool's fine control matters. AJohn Smith from the 'DIY Auto' magazine claims, "A Dremel gives you the freedom to sculpt your vision accurately, an essential in modern car customization."In terms of versatility, the choice of bits available caters to various needs — from thin cutting discs for detailed and intricate patterns, to reinforced ones for heftier cuts through robust materials.
Finally, the cost-effectiveness of opting for a Dremel over more specialized equipment can't be overstated. While professional-grade tools may carry daunting price tags, a Dremel serves as a valuable investment for both hobbyists and professionals alike. Beyond just cutting, a Dremel finds utility in sanding, polishing, and drilling, expanding its usefulness across countless other projects, saving time and money. It’s this multitasking capability, combined with its efficacy in cutting carbon fiber, that cements the Dremel's place on any enthusiast's workbench.
When you consider the factors, such as precise cuts, user accessibility, and wide-ranging uses, it's easy to see why a Dremel is the tool of choice for many tackling the complex and rewarding realm of carbon fiber projects. Enjoy the process—it might just surprise you how naturally satisfying cutting carbon fiber with a Dremel can be.
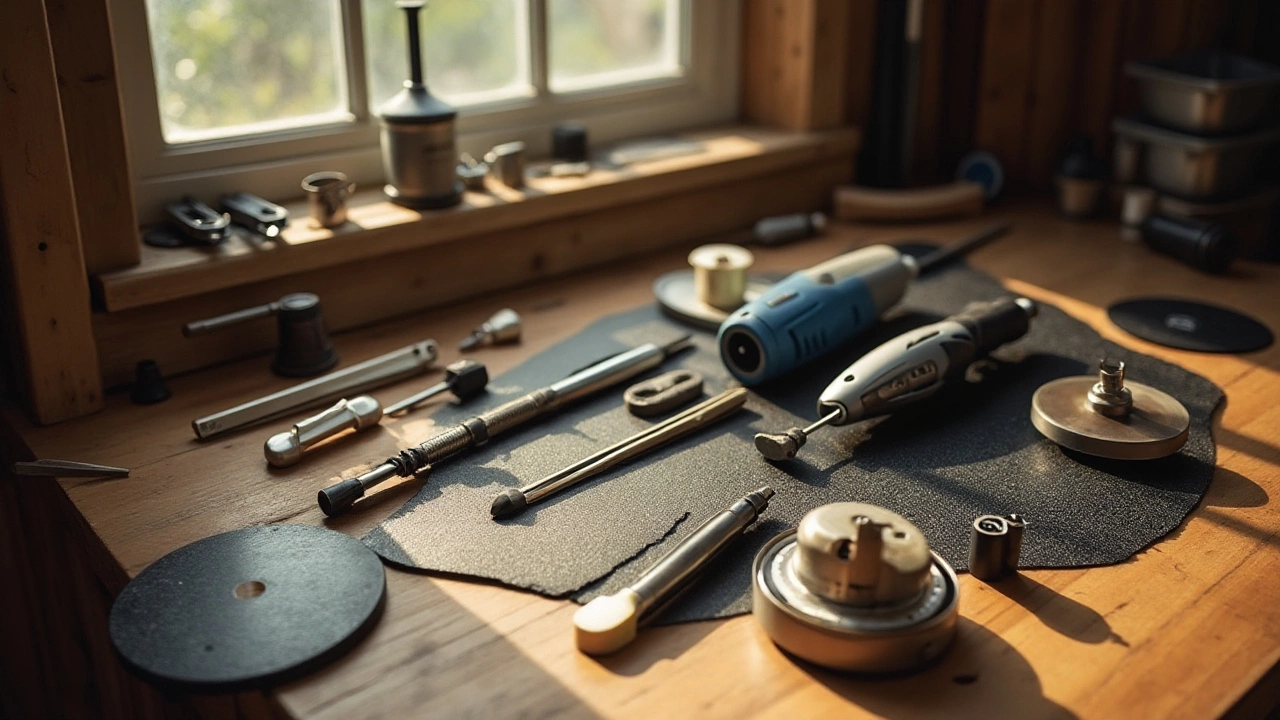
Step-by-Step Guide to Cutting Carbon Fiber
Stepping into the world of carbon fiber with a Dremel can feel akin to crafting magic with your hands, yet the process is grounded in scientific precision and care. Carbon fiber, with its woven fabric-like structure embedded in an epoxy resin, demands respect and understanding of its properties to be properly worked with. A Dremel, known for its versatility and power, is a tool that can cut through carbon fiber sheets efficiently when used with the right accessories and techniques. Let’s navigate the steps you need to undertake to slice through this material, ensuring not only efficiency but also a polished finish.
Initiating the cutting process starts by selecting the right cutting wheel for your Dremel. High-quality fiberglass reinforced cut-off wheels are recommended due to their ability to endure the rigidity and strength of carbon fiber. It’s important to note that turning on the Dremel should be followed by a gradual approach to the cutting line, applying a steady but gentle pressure. The feeling is akin to slowly slicing through a firm loaf of bread rather than hammering through a brick.
Before you start, ensure your work area is well-ventilated. This precaution cannot be stressed enough, as the dust generated is not only irritating but can also pose health risks. Wearing a mask equipped with a proper filter and protective eyewear should be non-negotiable—a simple step that ensures safety as you engage in your project.
"Safety isn't expensive, it's priceless." — Jerry Smith, renowned safety expert and advocate.
With your safety gear on, take the time to outline your cut precisely on the carbon fiber surface. Utilize masking tape to draw edges, as this helps reduce fraying while providing a clear guide to steer your Dremel accurately. A diamond-tipped cutting wheel is another excellent option for those particular about edge precision, though it tends to wear out faster than reinforced options.
Once you're set, turn on your Dremel and begin cutting at a steady pace. It is crucial not to force or rush through the material, which can lead to chipping and uneven edges. Let the tool do the work. Maintaining a consistent speed and pressure will give you a clean, smooth cut. Each cutting session should last no more than 10 minutes before pausing to prevent overheating the fibers, which might compromise the structural integrity or your Dremel tool.
After achieving the basic cut, refining the edges comes next. Using a fine-grit sanding attachment on the Dremel can help smoothen the edges, removing rough surfaces or minor snags left behind. Remember, in every facet of working with carbon fiber, patience is your ally. It's worth noting that polishing compounds, while seemingly optional, can significantly enhance the final appearance of the edges, lending the project a professional finish.
Here is a summarized table of tips for your cutting process:
Step | Tip |
---|---|
Tool Selection | Use high-quality reinforced wheels |
Safety | Wear mask and eyewear |
Precise Cutting | Outline with masking tape |
Finishing | Polish with compounds |
Carbon fiber projects not only challenge your craftsmanship but also reward you with lightweight, resilient components that scream precision engineering. Whether you’re fashioning a sleek spoiler or undertaking a home improvement project, cutting carbon fiber with a Dremel is a skill that, once mastered, opens doors to creativity and innovation.
Safety Measures When Working with Carbon Fiber
When working with carbon fiber, taking the right safety measures is crucial. The material, while highly advantageous due to its strength-to-weight ratio, poses certain risks during handling and cutting. It's essential to protect both yourself and your workspace to minimize any potential hazards. One of the critical steps when using a Dremel to cut carbon fiber involves understanding the dust that gets generated. These fine, lightweight particles can be harmful if inhaled over time, potentially leading to respiratory issues. Make sure you're operating in a well-ventilated area and wearing a suitable mask or respirator to keep those tiny particles at bay.
Along with respiratory protection, eye safety is another major factor. When you're cutting carbon fiber, fragments can fly in unpredictable directions. Always wear safety goggles to prevent any fragments from reaching your eyes. One might be tempted to skip this step, but in an unexpected incident, goggles can be the difference between a close call and a trip to the emergency room. A full-face shield provides additional protection and is worth considering, especially if the project involves prolonged cutting sessions.
Beyond personal protection, ensure your work space is organized. A cluttered environment invites accidents and makes it easier for tools or materials to get misplaced. Secure carbon fiber pieces firmly before cutting to prevent slips and aim for a stable surface. This not only protects you but also helps keep your cutting technique accurate, contributing to a professional finish. Remember, the strength of carbon fiber also makes it quite resistant to traditional cutting methods, which is why tools like a Dremel, equipped with the right bits, are recommended.
Lastly, let's touch upon proper attire and its importance. Loose clothing or dangling accessories can catch on tools, leading to accidents. Wear fitted clothing when working with power tools and consider wearing gloves designed for dexterity and grip. While gloves are debated due to potential risks of being caught in tools, selecting specially designed work gloves can mitigate many of these concerns. On this topic, Frank De Angelis, a senior engineer specializing in composite materials, said in a recent interview, "Having the right gear isn't about simply checking a box—it's about ensuring each safeguard works in harmony to eliminate all foreseeable risks."
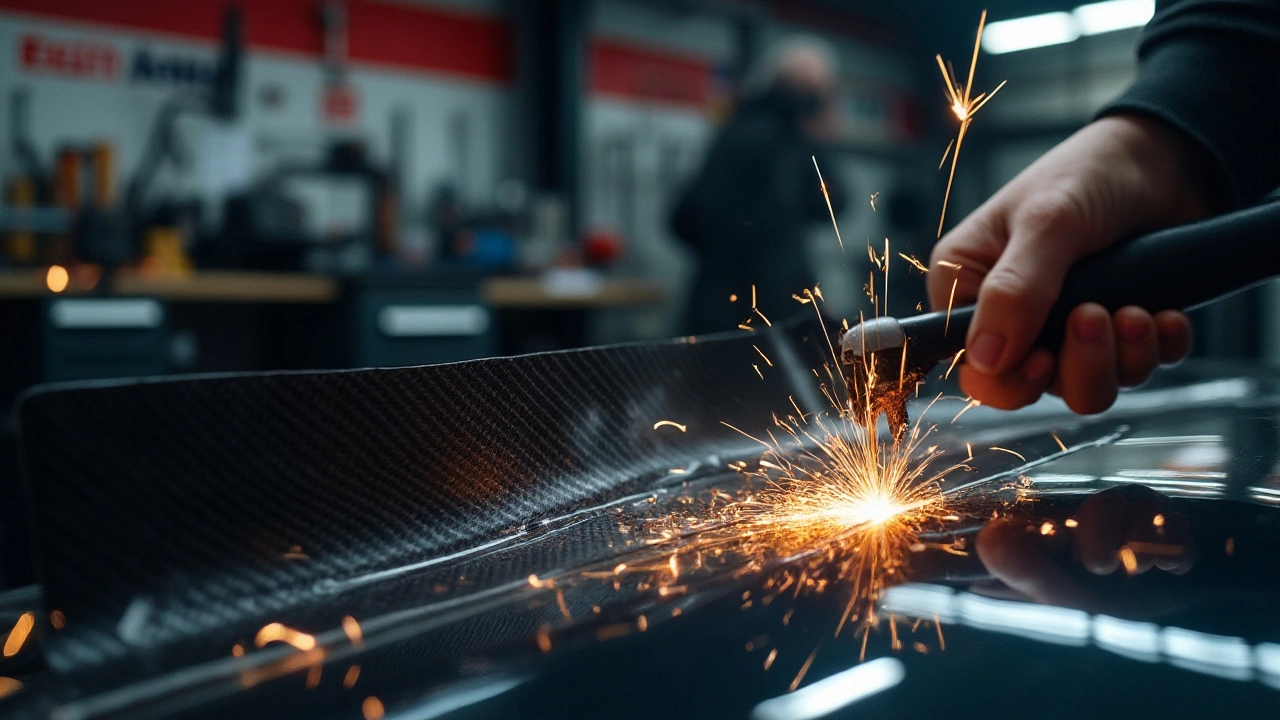
Finishing and Aftercare Tips
After successfully cutting your carbon fiber with a Dremel, the next crucial step is the finishing and aftercare process. It's important to achieve a smooth, professional look, as raw edges can detract from the material's aesthetic and performance advantages. Start by examining the edges closely to ensure they are even and free of burrs or fibrous strands. Using fine-grit sandpaper, manually sand the cut edges in a gentle motion to smooth out any rough areas. This is a meticulous process that requires patience, as an uneven edge can compromise not only the physical appearance but also the structural integrity of the piece, particularly in applications like spoilers where aerodynamics are key.
Once the edges are sanded to a satisfactory level, consider sealing them for added protection. A sealant will not only improve the visual appeal by providing a gloss finish but will also protect against moisture and environmental damage. Choose an epoxy resin or a clear coat specifically designed for carbon fiber application. Apply the sealant evenly, ensuring full coverage, and let it cure according to the manufacturer's instructions. It's a good practice to apply multiple layers for enhanced durability, lightly sanding between coats to ensure adhesion and smoothness. As you work, remember that temperature and humidity can affect drying times and the final finish quality, so monitor your environment closely.
After completing the finishing touches, proper aftercare will extend the life of your carbon fiber piece. Regular inspections for chips, cracks, and any signs of wear should be part of your maintenance routine. Cleaning should be done with a soft cloth and non-abrasive cleaner to avoid scratching the surface. Avoid exposing the carbon fiber to harsh chemicals or extreme temperatures, as these can degrade the material over time. Always follow up with a protective wax or polish to maintain the gloss and ensure ongoing protection from UV light, which could gradually fade the material.
"Maintaining the finished look of carbon fiber is as much about aesthetics as it is about protection," notes Dr. Anna Moore, a specialist in composite materials. "Regular, gentle care will allow you to enjoy the benefits of this advanced material for years to come."
To sum it up, the finishing and aftercare steps are not just a recommended practice; they are essential to preserve the structural and aesthetic value of your project. While many find the allure of carbon fiber in its immediate qualities post-cut, the true merit lies in the longevity ensured by these finishing processes. Whether you're customizing a vehicle part or crafting another intricate design, proper finishing and aftercare will ensure you're maximizing the benefits and lifespan of your work.